Replacing standard bin storage shelving with modular drawer cabinets or drawers in shelving units is one of the most effective ways to save space, increase speed and accuracy in order picking, and significantly reduce the time spent taking inventory. However, before you decide on a final layout, there are a few points to consider when designing your system that will make the change easier and ensure that your final layout will support growth and product changes in the future.
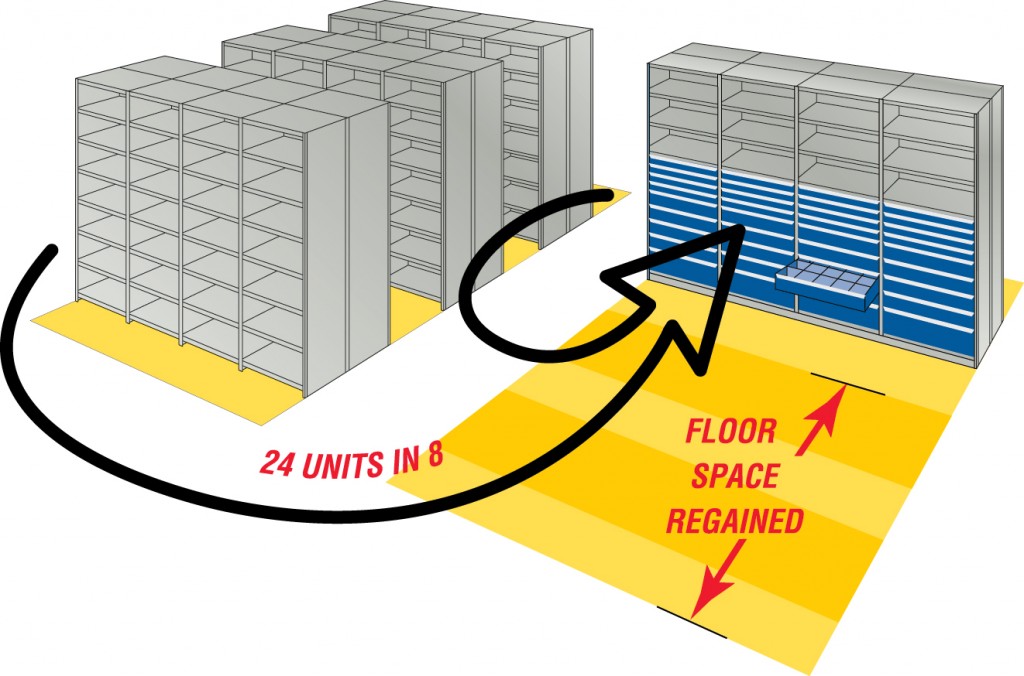
If your order picking software can assign an inventory item to any available space in your storage system, then your issues going forward will be minimal. This type of system offers the most flexibility in what locations are assigned to a specific product. Smaller products can be stored in a location with other small products, maximizing the efficiency of the storage space. New products can be added at the end of the system in empty drawers provided for growth or be placed in slots vacated by older stock. This type of software and organization will make it easier to change product lines, add products, and remove discontinued or obsolete products.
However, there are storage systems that can make the transition to drawer storage more difficult and create problems in the future. Let’s examine the typical concerns and see how these can be resolved with proper planning during the design phase.
Typical Storage Methods That Create Problems (and the best way to resolve the issue):
PROBLEM 1: Storing products in numerical sequence or grouped by vendor for ease in picking.
This is probably the most typical storage system, but it is not the most space efficient layout. It is easy to locate a part moving down the aisle, counting part numbers as you go. However, this creates two main problems. First, you often have large items on a shelf, right next to smaller ones. This forces your shelf spacing to be higher and wastes space around all the small items because of one larger item.
The second problem is when new items are added to the line that fall in the middle of a sequence of numbers. Now everything has to be moved ‘down one item’ to allow space for the new item. The reverse is true when an item is discontinued. You now have a gap in the system that is not used at all, wasting more space.

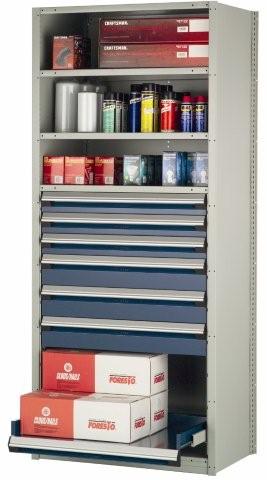
SOLUTIONS: Whenever possible, the most efficient storage is possible when you can store the same sized items together. It may be worth looking into a software system that allows you to reorganize your stock in this manner. If this is not an option, then modular drawers in shelving can provide a middle way solution. Installing drawers in shelving to fit smaller and then mid-sized products, larger products can be stored on the open shelves above and below the drawers. This allows you to keep part numbers in a ‘close to numerical’ sequence, with the full sequence being in a single shelving unit, but some of the larger items moved to the fixed shelves. This can increase storage efficiency significantly, so it can compensate for any difficulty in locating items that are slightly out of sequence.
PROBLEM 2: Keeping a certain class of products separate from others for security or quality control.
This is a common need in many stocking situations. There can be high value or dangerous products that may need to be locked up or secured in some way, separate from the regular inventoried items. Items that come in from a vendor may also need to be checked for quality or inspected before they can be put into the regular inventory.
SOLUTIONS: In situations that require a higher control of product accessibility and distribution, there are a several security options available with modular drawer systems. With drawer cabinets, there will be a single key that locks all the drawers at once. This can limit access to those authorized to handle the products or items in that cabinet. Key systems for multiple users and multiple cabinet locations are available with a master keyed system to allow a supervisor access to all locations. Drawers in shelving can be locked with a vertical security bar attached to the shelving unit that can lock each bank of drawers. Both lock systems are available with keyed locks or are adaptable for padlocks.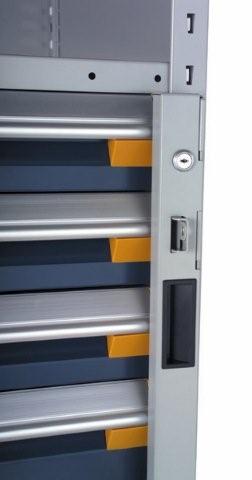
You can also have single drawers of a group, within a cabinet or in a shelving unit, which can be locked individually. These can be keyed differently from the cabinet or security bar, so that all the drawers in a group are accessible when unlocked, except for certain drawers that would require another key.
The highest security would be with a modular drawer cabinet that has a true One-Drawer-at-a-Time mechanism. This would prevent two drawers from being opened at once.
Locking doors are available that allow you to lock the entire contents of a standard shelving unit or a drawers-in-shelving unit. These doors come in solid steel or clear polycarbonate and are adaptable to any standard shelving, with or without drawers.
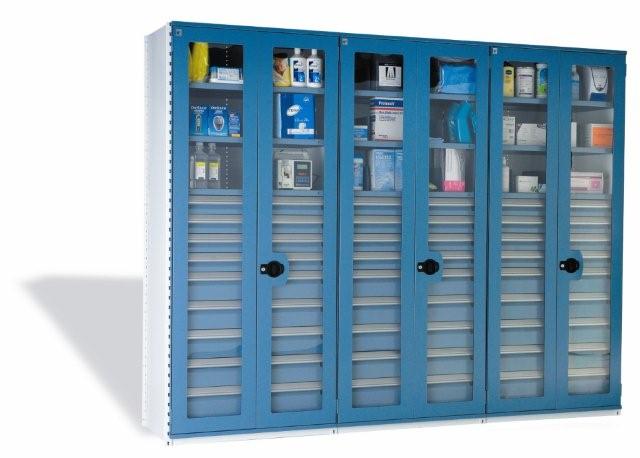
![[#Beginning of Shooting Data Section] Nikon D2Xs 2011/06/13 14:51:31.4 RAW (12-bit) Image Size: Large (4288 x 2848) Color Lens: 24-70 mm F/2.8 G Focal Length: 40 mm Exposure Mode: Manual Metering Mode: Multi-Pattern 1/250 s - F/9 Exposure Comp.: 0 EV Sensitivity: ISO 100 Optimize Image: White Balance: Preset Focus Mode: AF-S VR Control: OFF Long Exposure NR: OFF High ISO NR: Off Color Mode: Mode II (Adobe RGB) Tone Comp.: Normal Hue Adjustment: 0° Saturation: Normal Sharpening: Medium high Flash Mode: Optional, M x 1/8 (-2/3 EV) Flash Exposure Comp.: Flash Sync Mode: Front Curtain Bounce Flash Image Authentication: OFF Image Comment: [#End of Shooting Data Section]](https://smallpartspro.com/wp-content/uploads/2015/06/R5SSE-874806_61651-1024x905.jpg)
PROBLEM 3: Expiration dated or time sensitive stock that needs to maintain a First-In First-Out rotation.
Some products have a shelf life and need to be used or distributed within a certain amount of time. It is not acceptable to have older stock left in the back of a shelf that will eventually have to be discarded because it has passed its expiration date. Stock needs to be organized by date in a simple and clear way.
SOLUTION: There are several ways that drawers can help with this issue. Product can be assigned to a specific ‘lane’ within a drawer. Each lane can have a movable divider that can be placed behind existing stock to indicate a batch or time sensitive lot. Newer product can be added to the drawer behind the divider and then the divider removed or product moved to the front of the divider after all the older stock is gone. In larger volume situations, two lanes could be assigned to a single product with a label showing the date code of each group. Older product is chosen first and then when that lane is empty, it becomes available for the next group of fresher product.
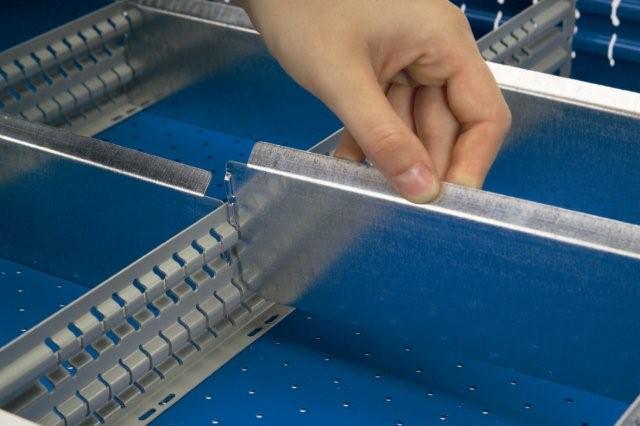
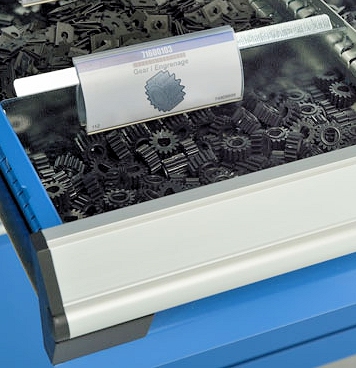
PROBLEM 4: Varying inventory levels by a large amount to adjust for seasonal or cyclical requirements.
Due to the seasonal nature of the need for some products, inventory levels can be very high at one time of the year and then drop to a minimum maintenance level for the rest of the year. When this happens with several items in your product line, it can create problems in storage and stock rotation.
SOLUTION: Drawers in Shelving allows for dense and efficient storage in the drawers, while providing shelves above or below the drawer set to accommodate overstock of the same items. Color codes, tags, or a secondary label in the drawer labeling system can be used to indicate that there is overstock for a specific item and give the location of where to find the overstock. The dividers in the compartments can accept a variety of label widths and sizes to help with this type of system.
PROBLEM 5: Your product line is growing and you will be continually adding new products.
Growth is a good thing in most businesses, but can be difficult if the additional items added to your product line are not included in your planning. This usually leads to the disruption of your regular storage system and inefficient temporary storage options.
SOLUTIONS: You can factor in growth with modular drawers in a number of ways. For items that need to be grouped with other similar items, we can leave space in drawers to allow for the addition of new items in that group. An analysis of your product mix will dictate how much space should be made available, but typically 20% of the space in a drawer can be reserved in high growth markets.
With the conversion of standard shelving to modular drawers in shelving, planning for growth is easier. Drawer sets can be added in groups from 18” to 48” high. So, typically you could start with 24” of drawers in a shelving unit (say, 5 or 6 drawers and add another 12” or 24” of drawers as the need for more high density storage arises.
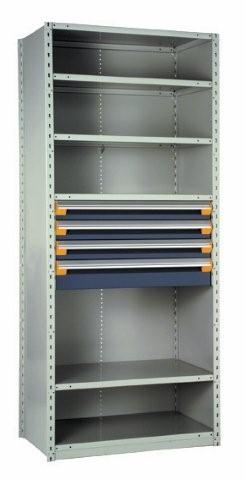
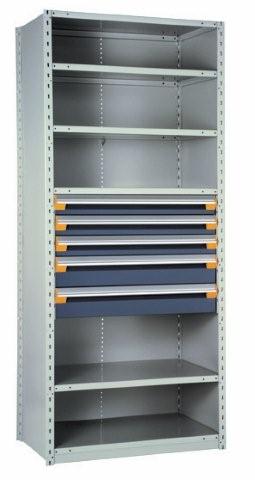
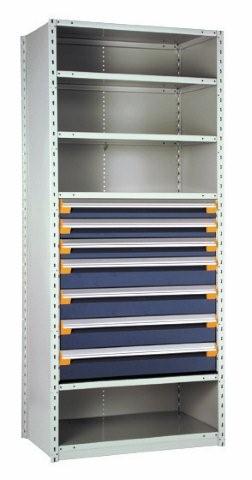
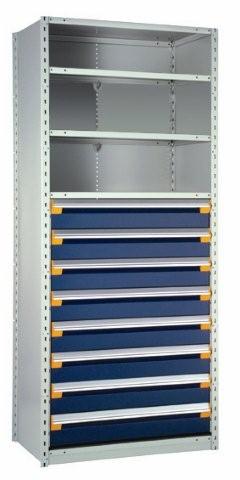
When converting to modular drawers, because of the efficiency of the drawer system, there will typically be empty shelving units left at the end of the process. These can be used for bulk storage or overstock and then converted to drawers in shelving when the existing system has reached its capacity.
These are just some of the ideas that you can use to plan for the future and ensure that your storage system will adapt as your business grows and changes. Call us or email with any questions you have about your specific storage problems: support@innovostorage.com
Click Here for more information on 5s organization.
Innovo Storage Systems 1 Goldsmith St, Johnston, RI 02919 (401) 383-0883